The soaring demand for solar energy has transformed manufacturing plants from million-dollar ventures into billion-dollar megafactories, revolutionizing how we produce clean energy technology. Modern solar panel manufacturing facilities represent a critical investment in our sustainable future, with costs ranging from $100 million for basic assembly plants to over $1 billion for advanced facilities that produce everything from raw silicon to finished panels. These facilities dramatically influence the final cost of residential solar installations, typically accounting for 30-40% of the panels’ retail price.
Yet, despite substantial upfront costs, manufacturing innovations and economies of scale continue driving down production expenses. Today’s state-of-the-art facilities produce panels at less than 70 cents per watt – a remarkable 90% reduction from a decade ago. For homeowners considering solar installation, understanding these manufacturing economics reveals why panel prices keep falling and explains how choosing the right time to invest can lead to significant savings.
Breaking Down Solar Manufacturing Plant Costs
Initial Setup and Equipment Costs
Setting up a solar panel manufacturing plant requires significant upfront investment in facilities and equipment. A typical medium-sized plant needs about 50,000 square feet of space, with facility construction costs ranging from $2-4 million. The production line itself demands sophisticated machinery, including automated assembly systems ($1.5-2 million), solar cell testing equipment ($500,000-750,000), and lamination machines ($300,000-500,000).
Essential technology investments include quality control systems ($200,000-400,000) and inventory management software ($50,000-100,000). Clean room facilities, crucial for maintaining product quality, typically cost between $750,000 and $1 million. Other necessary equipment includes panel framers, junction box assemblers, and packaging systems, collectively adding another $1-1.5 million to the setup costs.
The total initial investment for a medium-sized plant usually falls between $7-10 million, though costs can vary based on location and production capacity. This investment directly influences the final cost of solar panels, but improved manufacturing efficiency and technology advances continue to drive down these expenses, making solar energy more affordable for homeowners.
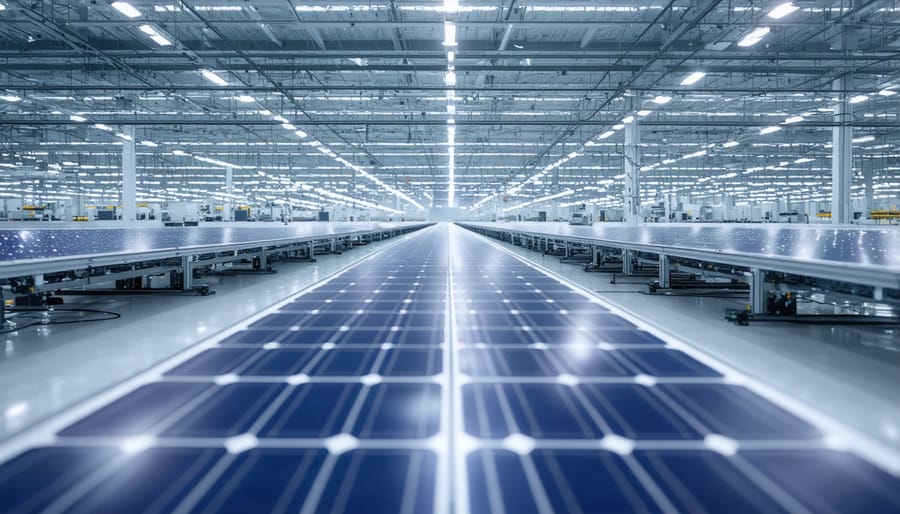
Operational Expenses
The day-to-day operation of a solar panel manufacturing plant involves several ongoing expenses that directly influence the final cost of solar panels. Labor costs typically represent 20-30% of operational expenses, including skilled technicians, quality control specialists, and production line workers. Raw materials, primarily silicon, glass, and metal components, account for approximately 40-50% of recurring costs, with prices fluctuating based on market conditions and supply chain factors.
Maintenance and equipment upkeep form another significant expense category, usually ranging from 10-15% of operational costs. This includes regular machinery servicing, replacement parts, and periodic upgrades to maintain production efficiency. Utility expenses, particularly electricity for running the manufacturing equipment, can consume 5-10% of the operational budget.
Quality control processes and certification requirements add another layer of expenses, typically accounting for 5-8% of operational costs. These measures are essential for ensuring panels meet industry standards and performance specifications. Transportation and logistics expenses round out the operational costs, varying between 5-10% depending on the facility’s location and distribution network.
How Manufacturing Costs Affect Your Installation Price
Price Components Breakdown
The manufacturing costs of solar panels significantly influence solar panel installation costs for homeowners. Raw materials, particularly silicon and specialized glass, typically account for about 40% of manufacturing expenses. Labor and equipment costs in the production facility make up roughly 30%, while quality control testing and certification processes contribute another 15%. The remaining costs include research and development, facility maintenance, and packaging.
Manufacturing efficiency plays a crucial role in determining final consumer prices. Modern automated production lines have helped reduce labor costs, while improved silicon processing techniques have lowered material expenses. These advancements have contributed to a steady decrease in solar panel prices over the past decade.
Energy consumption during manufacturing represents another significant cost component, typically accounting for 10-15% of total production expenses. However, many manufacturers are now using renewable energy in their facilities, which helps reduce both costs and environmental impact.
The good news for homeowners is that increased competition and technological improvements continue to drive down manufacturing costs, making solar energy more affordable each year. These savings are regularly passed on to consumers, resulting in more accessible clean energy solutions for residential installations.
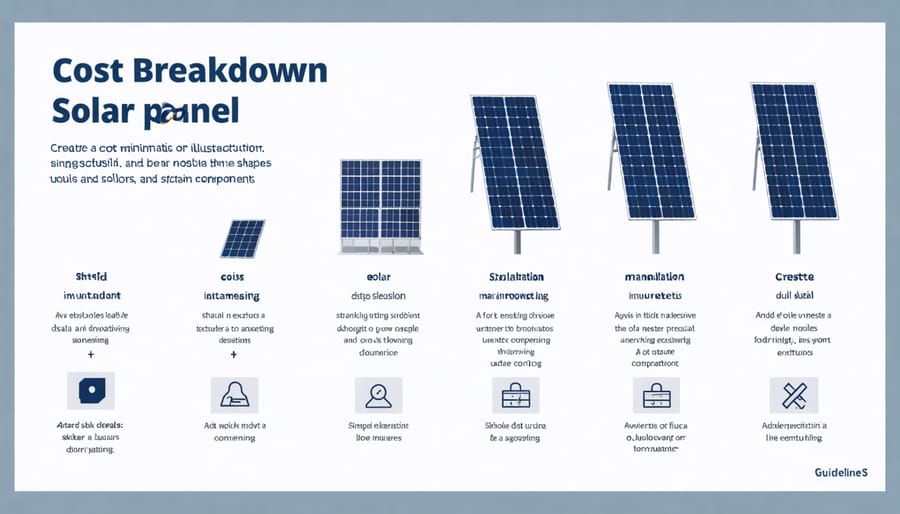
Cost Reduction Trends
Manufacturing costs for solar panels have seen a remarkable downward trend over the past decade, directly benefiting homeowners considering the investment value of solar panels. Improved automation, more efficient production processes, and economies of scale have led to significant cost reductions in manufacturing facilities worldwide.
The introduction of advanced robotics and artificial intelligence in production lines has streamlined operations, reducing labor costs and minimizing production errors. Additionally, manufacturers have optimized their supply chains and material usage, cutting waste and lowering raw material expenses. These improvements have resulted in a steady decrease in production costs, with savings passed on to consumers.
Recent innovations in silicon wafer production and cell efficiency have further reduced manufacturing expenses. The development of larger wafers and better cell designs means more power output per panel, effectively lowering the cost per watt for homeowners. Manufacturing plants are also implementing energy-efficient practices, reducing their operational costs and environmental impact.
Industry experts predict this trend will continue, with new technologies and manufacturing techniques emerging regularly. For homeowners, this means more affordable solar installations and faster returns on investment, making solar energy an increasingly attractive option for sustainable living.
Future Manufacturing Innovations and Cost Savings
Emerging Technologies
New manufacturing technologies are revolutionizing how solar panels are made, making them more affordable for homeowners. One of the most exciting developments is perovskite solar cells, which can be printed like newspapers using roll-to-roll manufacturing. This process dramatically reduces production costs and energy consumption compared to traditional silicon-based manufacturing.
Automated production lines with artificial intelligence and robotics are also transforming factory operations. These smart systems minimize waste, increase efficiency, and ensure consistent quality, ultimately leading to lower production costs that benefit consumers.
Another breakthrough is the development of ultra-thin solar cells that use significantly less raw material while maintaining high energy conversion rates. Manufacturers are also exploring recycled materials and simplified assembly processes that cut down on production expenses without compromising panel performance.
3D printing technology is making its way into solar manufacturing, allowing for custom panel designs and reduced transportation costs through localized production. Meanwhile, new coating technologies are extending panel lifespan and improving efficiency, offering better value for homeowners’ investments.
These innovations aren’t just making panels cheaper to produce – they’re also creating more durable and efficient products. As these technologies mature and become widely adopted, experts predict a continued decline in solar panel prices, making sustainable energy more accessible to everyone.
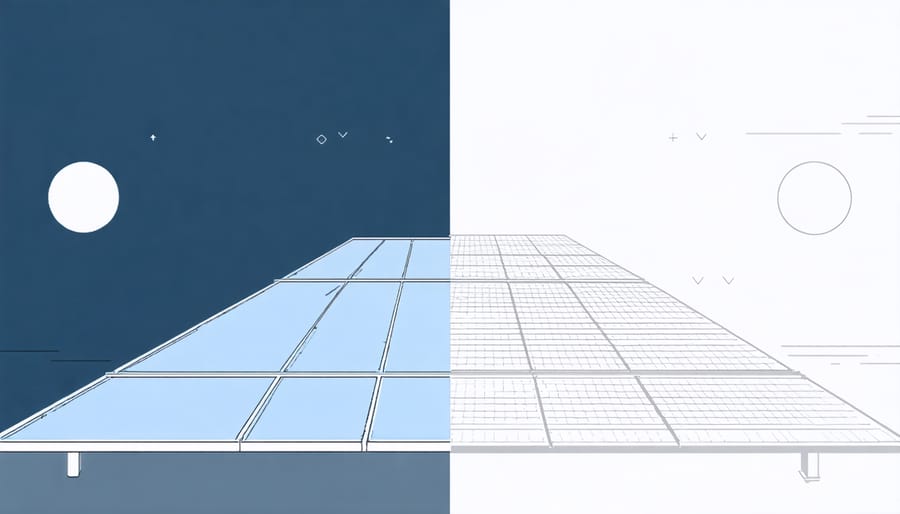
Consumer Benefits
As manufacturing efficiency improves and production scales up, homeowners stand to gain significant benefits from declining solar panel prices. These cost reductions directly translate to lower installation expenses for residential solar systems, making sustainable energy more accessible to the average homeowner.
The streamlined manufacturing processes and automated production lines are reducing labor costs and material waste, resulting in savings that manufacturers can pass on to consumers. Homeowners can now expect to pay 40-50% less for solar installation compared to prices from just a decade ago. This dramatic decrease makes the return on investment significantly more attractive, with many households now able to recoup their solar investment within 5-8 years.
Additionally, as manufacturing plants become more efficient, the quality and reliability of solar panels continue to improve. Modern panels offer better energy conversion rates and longer warranties, providing homeowners with more value for their investment. The increased competition among manufacturers also drives innovation, leading to more advanced features and improved performance without raising costs.
These manufacturing improvements also contribute to faster installation times and reduced labor costs, as standardized components and better design make the installation process more straightforward. For homeowners, this means less disruption during installation and lower overall project costs.
The relationship between solar panel manufacturing costs and consumer benefits creates a win-win situation for both industry and homeowners. As manufacturing facilities become more efficient and automated, production costs continue to decrease, leading to more affordable solar panels for residential installations. These cost reductions are directly passed on to homeowners, making solar energy increasingly accessible to the average household.
The long-term savings are particularly compelling. While manufacturing plants require significant initial investment, their efficiency improvements and economies of scale contribute to steadily declining solar panel prices. For homeowners, this means lower upfront installation costs and faster return on investment through reduced electricity bills. Current trends suggest that solar panel prices will continue to drop, making the technology even more attractive for budget-conscious consumers.
Furthermore, as manufacturing processes become more refined and sustainable, the environmental benefits multiply. Modern production facilities are increasingly powered by renewable energy themselves, creating a truly sustainable cycle that benefits both the planet and consumers’ wallets. This positive trend in manufacturing efficiency ensures that solar power remains a smart, future-proof investment for homeowners seeking energy independence and reduced utility costs.